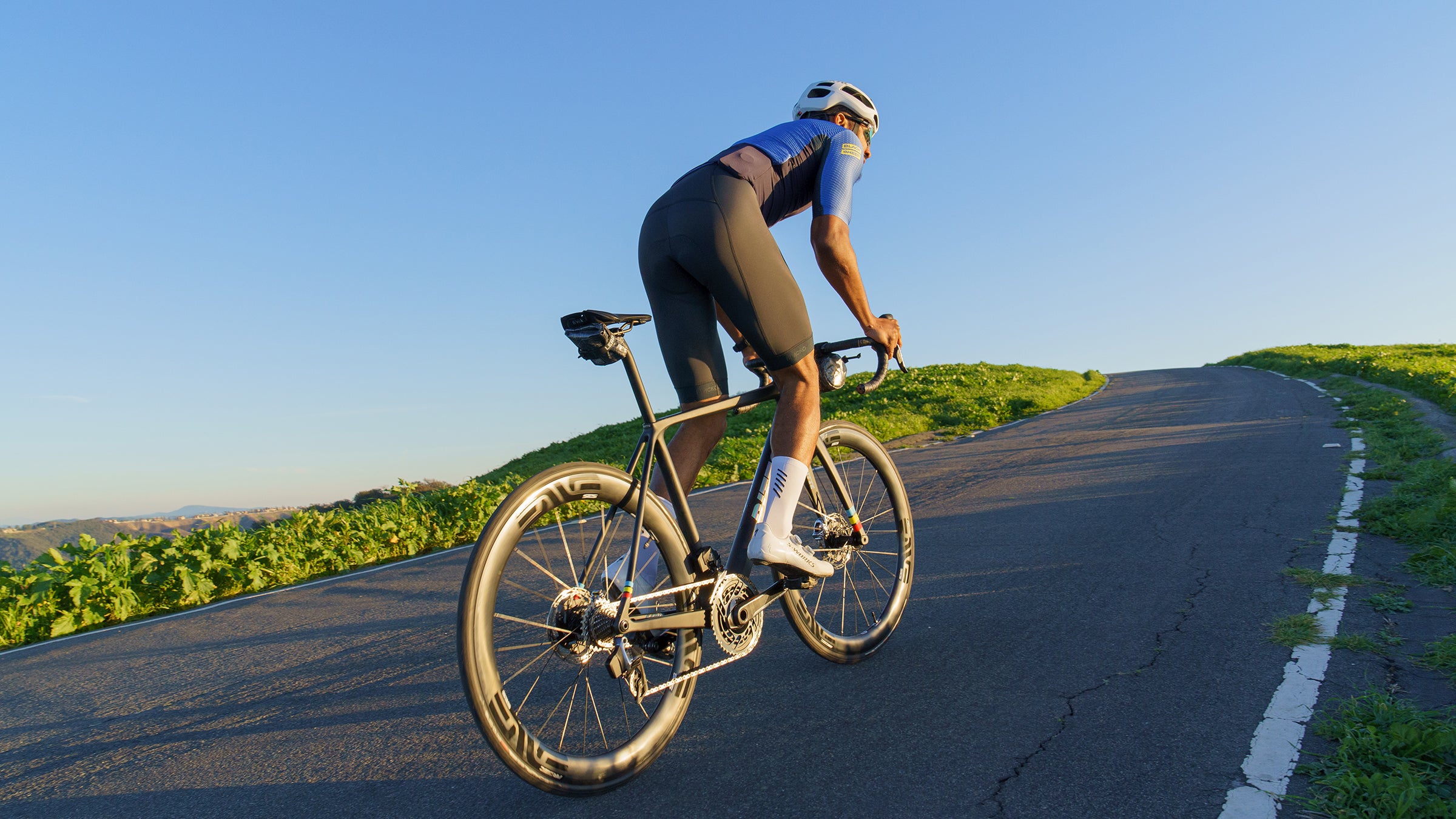
Bike product testing is a multifaceted process crucial for ensuring that bicycles meet rigorous standards of safety, performance, and durability. The rise in cycling popularity has increased the demand for high-quality bikes, making thorough testing essential for manufacturers to guarantee their products’ reliability. Effective bike product testing employs a variety of methods and tools, each designed to evaluate different aspects of a bike’s functionality and integrity. Understanding these methods and tools provides insights into how manufacturers achieve the high standards expected by today’s cyclists.
One of the primary methods of bike product testing is impact testing. This involves subjecting the bike frame and components to sudden, forceful impacts to simulate real-world crashes or falls. Impact tests are critical for identifying potential weak points in the frame and ensuring that the bike can withstand significant shocks without catastrophic failure. For instance, frames are often dropped from a certain height with weights attached to mimic the forces experienced during a crash. This helps ensure that the frame can absorb impacts and protect the rider in the event of an accident.
Fatigue testing is another essential method used in bike product testing. This type of testing subjects the bike to repeated cycles of stress to simulate long-term usage. During fatigue testing, components such as frames, handlebars, and wheels are repeatedly loaded and unloaded to mimic the stresses they would endure over many rides. This helps to identify any weaknesses that might develop over time, ensuring that the bike remains reliable and safe even after extensive use. Fatigue testing is particularly important for high-performance bikes, which are often pushed to their limits by competitive cyclists.
Static load testing is also crucial for evaluating the structural integrity of bicycles. In static load tests, a constant load is applied to various parts of the bike to ensure they can bear weight without deforming. This type of testing assesses the bike’s ability to support the rider’s weight and any additional forces that might be encountered during use, such as carrying gear or hitting bumps. By applying loads to the frame, fork, and other critical components, manufacturers can verify that their bikes are capable of handling real-world stresses without compromising safety or performance.
The testing of individual components, such as wheels, brakes, and drivetrains, is another critical aspect of bike product testing. Wheel testing involves assessing the rims, spokes, and hubs for their ability to endure impact and rotational forces. This ensures that the wheels can handle the rough terrain and provide a smooth ride. Brake testing evaluates the stopping power and reliability of the braking system, often under various conditions, including wet and dry environments. This is crucial for ensuring that the brakes can perform effectively in different weather conditions. Drivetrain testing focuses on the efficiency and durability of components like the chain, gears, and derailleurs, ensuring smooth shifting and long-lasting performance.
Regulatory standards play a significant role in bike product testing. In the United States, the Consumer Product Safety Commission (CPSC) sets guidelines for bike safety, including requirements for frame strength, brake performance, and reflectivity. In Europe, the European Committee for Standardization (CEN) establishes similar standards. Compliance with these regulations is mandatory, and manufacturers must conduct thorough testing to verify that their products meet these criteria. This regulatory compliance ensures that bikes are safe for consumers and helps prevent accidents caused by substandard equipment.
Electric bikes (e-bikes) require additional testing due to their electrical components. Battery safety is a primary concern, as lithium-ion batteries can pose risks if not properly managed. Battery tests involve assessing the capacity, charging and discharging cycles, thermal management, and safety mechanisms to prevent overheating or short-circuiting. Motor performance testing ensures that the electric assist provides consistent power and operates efficiently under various conditions. Additionally, the integration of electronic systems in e-bikes necessitates thorough testing of sensors, controllers, and displays to ensure they function correctly and withstand environmental stresses.
Field testing is a critical component of bike product testing that complements laboratory tests. While lab tests provide valuable data on the structural integrity and performance of a bike, field testing offers real-world insights. Professional riders and experienced testers use the bikes in various environments, including off-road trails, urban settings, and long-distance routes. This helps identify practical issues that may not emerge in controlled lab conditions, such as handling, comfort, and durability over time. Field testing provides a comprehensive evaluation of the bike’s performance in real-world conditions, ensuring that it meets the needs and expectations of cyclists.
User feedback is another invaluable tool in the bike product testing process. Manufacturers often gather reviews and conduct surveys with customers who have purchased and used their bikes. This feedback helps identify any recurring issues or areas for improvement that might not have been detected during initial testing. By incorporating user experiences, manufacturers can refine their designs and address practical concerns, enhancing the overall quality and reliability of their bikes. This continuous feedback loop is essential for maintaining high standards and ensuring customer satisfaction.
Technological advancements have significantly influenced bike product testing methods. Modern bikes often use advanced materials such as carbon fiber and high-strength alloys, which require specialized testing techniques. For example, carbon fiber frames need to be tested for delamination and structural integrity, as their failure modes differ from those of traditional metal frames. Additionally, the use of computer simulations and finite element analysis (FEA) allows engineers to model and test bikes virtually. These tools enable the identification of potential weak points and optimization of designs before physical prototypes are built, reducing development time and costs while improving accuracy.
Sustainability is an emerging focus in bike product testing. As consumers become more environmentally conscious, manufacturers are striving to minimize the environmental impact of their products. This includes using sustainable materials, reducing waste in the manufacturing process, and ensuring the longevity of the bikes. Tests that assess the recyclability of materials, the environmental impact of production processes, and the overall lifecycle of the bike are becoming more common. Sustainable practices benefit the environment and appeal to eco-conscious consumers, enhancing the brand’s reputation and marketability.
Despite the rigorous testing processes, it is impossible to anticipate every potential issue that may arise during a bike’s lifespan. This highlights the importance of ongoing quality control and post-market surveillance. Manufacturers must conduct regular inspections and respond swiftly to any safety concerns that arise. Recalls and safety notices are sometimes necessary when defects are discovered after the bikes have been sold. A robust post-market strategy ensures that any issues are addressed promptly, maintaining consumer trust and safety.
In conclusion, effective bike product testing is essential for ensuring the safety, performance, and durability of bicycles. Through a combination of impact, fatigue, and static load testing, as well as evaluations of individual components and regulatory compliance, manufacturers can identify and address potential issues. Field testing and user feedback provide real-world insights that complement laboratory data, while technological advancements and sustainability considerations continue to shape testing methods. This comprehensive approach to testing ensures that bikes meet the high standards expected by today’s cyclists, providing a reliable and enjoyable riding experience. As the cycling industry evolves, so too will the methods and tools used in bike product testing, ensuring that the needs of cyclists are met and exceeded.
General FAQs.
General FAQs on Top Methods and Tools for Effective Bike Product Testing
What are the main methods used in bike product testing?
Bike product testing primarily involves impact testing, fatigue testing, and static load testing. Impact testing subjects the bike frame and components to sudden, forceful impacts to simulate real-world crashes or falls, ensuring they can withstand significant shocks. Fatigue testing involves repeated cycles of stress to mimic long-term usage, assessing the durability of components over time. Static load testing applies constant loads to various parts of the bike to verify their ability to support weight without deforming. These methods are essential for identifying and addressing potential weaknesses in bike designs.
How do manufacturers test individual bike components like wheels and brakes?
Manufacturers perform specific tests on individual bike components to ensure their performance and reliability. Wheel testing assesses the rims, spokes, and hubs for their ability to endure impact and rotational forces, ensuring durability and smooth operation. Brake testing evaluates the stopping power and reliability of braking systems under different conditions, such as wet and dry environments, to ensure they perform effectively in various weather scenarios. Drivetrain testing focuses on the efficiency and durability of components like the chain, gears, and derailleurs, ensuring smooth shifting and long-lasting performance.
What role do regulatory standards play in bike product testing?
Regulatory standards are crucial in bike product testing as they ensure that bicycles meet specific safety criteria set by governing bodies. In the United States, the Consumer Product Safety Commission (CPSC) establishes guidelines for aspects like frame strength and brake performance. In Europe, the European Committee for Standardization (CEN) sets similar standards. Compliance with these standards is mandatory, and manufacturers must conduct thorough testing to verify their products meet these criteria. Adhering to regulatory standards protects consumers and helps prevent accidents caused by substandard equipment.
How is testing for electric bikes (e-bikes) different from traditional bikes?
Testing for electric bikes (e-bikes) includes additional evaluations due to their electrical components. Battery safety is a primary concern, involving tests for capacity, charging cycles, thermal management, and safety mechanisms to prevent overheating or short-circuiting. Motor performance testing ensures the electric assist provides consistent power and operates efficiently under various conditions. E-bikes also undergo testing of their integrated electronic systems, such as sensors, controllers, and displays, to ensure they function correctly and withstand environmental stresses.
Why is field testing and user feedback important in the bike testing process?
Field testing and user feedback are vital as they provide real-world insights that complement laboratory data. Field testing involves professional riders and experienced testers using the bikes in various environments to identify practical issues like handling, comfort, and durability over time. User feedback, gathered through reviews and surveys, helps manufacturers uncover recurring issues or areas for improvement that might not be detected during initial testing. Incorporating real-world experiences into the testing process ensures that bikes meet the needs and expectations of cyclists, leading to higher satisfaction and reliability.